Parmak Freze ve Frezeleme Sorun Giderme Kılavuzu
Bu Yazıyı Dinleyebilirsiniz.
Bir parmak frezenin takım ömrünü belirleyen, kullanımı, malzeme özelliği ve kaplamasıdır. Operatörlerin sıkça karşılaştığı erken aşınma ve takım kırılması, aslında kolayca önlenebilir sorunlardır. Bu önlenebilir sorunlar, kötü parça kalitesine, makinenin çalışmama süresine ve hatta işlenen parçaların hurdaya çıkmasına dahi neden olabilir. Bu takımların iş milinde çalışırken karşılaştığı sorunları anlamak, bu gibi sorunlarla karşılaşanlar için sorun gidermek adına önemli bir ilk adımdır.
Takım ömrü hakkında bu makalemizi okumak ister misiniz? >> Takım Ömrünü Uzatmak İçin Neler Yapılabilir?
Takım Aşınması
Erken Takım Aşınması
Nedenleri
Bir operatörün herhangi bir işlem esnasında karşılaşabileceği en yaygın sorunlardan biri parmak frezede erken takım aşınmasıdır. Takım aşınması, genellikle kesme hızları takım için önerilen değerlerden yüksek olduğunda ya da ilginç bir şekilde parmak frezenin hız ya da beslemesi çok düşük olduğunda ortaya çıkabilir.
Ayrıca işlenen malzemenin sertliği ya da doğal bir aşındırıcı olması da uygun kaplama kullanılmamış kesici takımlara kolaylıkla zarar verebilir. Kaplamalar, kesici takım ve kesme işlemi için aşınma direnci sağlamak ve verimliliği artırmak da dâhil olmak üzere çeşitli işlevlere sahiptir.
Erken aşınma ile karşılaşılmasına neden olan diğer yaygın nedenlerden bazıları, yanlış helis açılarının kullanımı ve talaşların yeniden kesilmesidir.
Çözüm Önerileri
Bu sorunlar aslında çözümü basit sorunlardır. Kesme hızı ve ilerlemenin yanlış olması gibi durumlarda, operatörün başvurabileceği farklı seçenekler bulunur. Öncelikle iş mili hızını azaltmak, kesme hızındaki hatayı düzeltecektir. Sonrasında, üreticilerin hız ve besleme önerilerini barındıran çizelgeler gözden geçirilerek hız ve beslemeleri ayarlamak, uygun takım kullanımına olanak tanıyacaktır. Bu durum aynı zamanda talaş kesme sorunlarını da çözmeye yardımcıdır. Parçadaki talaşların düzgün bir şekilde temizlenmesi adına kesme derinliği ya da soğutma sıvısı/havayı ayarlamaya yardımcı olur. Son olarak, parça için uygun helis açısı ve kaplamanın tercih edilmesi, kesici takımın hem performansını hem de kullanım ömrünü olumlu yönde etkileyecektir.
Parmak Freze Kenar Deformasyonu
Nedenleri
Genellikle agresif ve rijit işlemede karşılaşılan kenar deformasyonu sorunu, hem devam eden işlemede hem de ilk kesimde ilerleme hızları çok agresif olursa karşılaşılan bir sorundur. Agresif kesme derinliği, takım kenar deformasyonunun oluşmasında bir diğer yaygın nedendir.
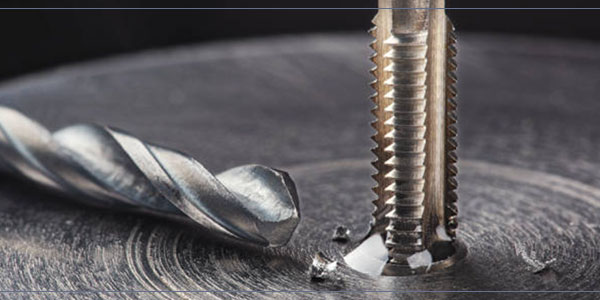
Parmak Freze Kenar Deformasyonu
Çözüm Önerileri
Kenar deformasyonu, operatörlerin kolayca çözüm bularak engelleyebileceği bir sorundur. Genel ve başlangıç hızları azaltılarak kesimin agresifliği azaltılabilir. Bununla beraber eksenel ya da radyal kesme derinliği azaltılarak, aşırı agresif takım yolları sorunu çözüme kavuşturulabilir.
Takımın kendinden kaynaklı bir sertlik sorunu varsa, takım tutucuların değiştirilmesi, takım sapının daha derin tutulması ya da daha kısa bir takım kullanılması gerekebilir. Parçanın yeniden sabitlenmesi veya genel kurulumda yapılacak iyileştirmeler de sorunu çözmede yardımcı olabilir. Son olarak, operatörlerin herhangi bir işlemde, makine millerinde salgı olup olmadığını kontrol etmesi gereklidir.
Freze Kırılması
Takım Kırılması
Nedenleri
Takım kırılması, kenar deformasyonuna benzer şekilde agresif ilerleme hızları ve aşırı kesme derinlikleri yüzünden gerçekleşebilir. Yine benzer şekilde, aşırı takım kullanma mesafesi, takım kırılması sorununda büyük pay sahibidir. Talaş birikmeleri de takım çatlakları ve kırılmalar üzerinde etkili bir faktördür. Aşırı derecede aşınmış bir parmak frezenin kullanımı da kırılmanın bir başka birincil nedenidir.
Çözüm Önerileri
Takım kırılma sorunlarını gidermenin en önemli yöntemlerinden biri ilerleme hızı ve eksenel / radyal kesme derinliğini azaltmaktır. Bu, seçilen takım yapısının belirlenen takım yolları için yetersiz, belirlenen parametrelerin ise çok agresif olduğu anlamına gelir. Sarkma gibi sorunlar yaşanıyorsa, takım şaftı daha derin tutulmalı ve mümkünse daha kısa bir takım tercih edilmelidir.
Talaş birikmesini önlemek adına hızları ve beslemeleri ayarlamak, talaşları düzgün şekilde uzaklaştırmak için soğutma sıvısı ya da hava basıncını artırmak gibi çeşitli çözümler değerlendirilmelidir. Daha az kanala sahip ve daha derin oluklu takımlarda talaş temizliği daha kolaydır. Bu gerçekten yola çıkarak, daha az kanala sahip bir takımın tercih edilmesi ile talaş birikmesi önlenebilir. Son olarak, bir takımı erkenden taşlamak da aşırı aşınma nedeniyle meydana gelen takım kırılmalarını engelleyecektir.
Talaş Birikmesi
Nedenleri
Talaş birikimi takım kırılmalarında itici bir güçtür. Bu nedenle bu sorunu erkenden çözmek, işleme operasyonunda başarının anahtarıdır. Bu durum, takım yeteneklerin üstünde agresif hız ve ilerlemeler kullanıldığında meydana gelir. Ayrıca takım olukları üretilen talaşa göre çok küçük olduğunda da birikmeler oluşacaktır. Son olarak, kullanılan soğutma sıvısının hacmi ve basıncı yetersizse, talaşların düzgün şekilde tahliye edilmesini sağlayamaz.
Talaş Birikmesi
Çözüm Önerileri
Operatör işlem öncesinde üretici tarafından sunulan hız ve besleme çizelgelerini incelemeli ve bu değerleri azaltmayı düşünmelidir. Daha az kanala sahip bir parmak freze de daha önce bahsettiğimiz gibi talaşların düzgün şekilde tahliye olmasını sağlayarak birikmeleri engelleyecektir. Soğutucu sıvı hacminin ve basıncının artırılması ve beraberinde kesme noktasına yakın bir konuma getirilen nozülle birlikte uygun tahliyenin gerçekleşmesine yardımcı olacaktır.
Titreşim
Nedenleri
Takım titreşimi, makinedeki bir parçanın hurdaya çıkmasının en kolay yollarından biridir. Kırılma öncesi titreşim meydana gelebildiğinden, sorunun çözümleri de birbirine oldukça benzer. Titreşimleri tamamen bertaraf etmek mümkün değildir fakat işleme operasyonunun beklentileri karşılaması için mümkün olan en alt seviyeye indirmek çok önemlidir.
İş milinde meydana gelen takım titreşimlerinin rijitlik ve agresif takım yolları gibi nedenleri bulunur. Rijitlikte yaşanan bu eksiklik, takımın kendisi ile sınırlı olmamakla birlikte ayrıca parça ve takım tezgahındaki etkenlere de atfedilebilir. Ayrıca, yanlış takım geometrisinin tercihi, gereksiz titreşim sorunlarına neden olabilir.
Çözüm Önerileri
Takım titreşim ve seslerini çözmenin en önemli yollarından bazıları; eksenel ya da radyal kesme derinliği ve ayrıca hız ve ilerlemeleri azaltmaktır. Sorunun nedeni zayıf rijitlik ise, sorunun kaynağı operatör tarafından belirlenmelidir. Takım tutucunun değiştirilmesi, takım sapının daha derin tutulması ya da daha kısa takım tercih edilmesi gibi çözümler uygulanabilir. Rijitlik sorunu ile karşılaşıldığında ayrıca makine milleri kontrol edilmelidir. Son olarak, parçanın yeniden sabitlenmesi ya da genel kurulumda yapılacak iyileştirmeler de sorunun çözümüne katkı sağlayabilir.
Çapaklar
Nedenleri
Talaşlı imalatta çapaklar oldukça yaygındır ve işlem sonunda operatör tarafından parça üzerindeki çapaklar özenle alınır. Bu yaygın bir durum olmakla birlikte, aşırı çapak oluşumunun birkaç nedeni vardır. Öncelikle, işlemede kullanılan yanlış hız ve ilerlemeler, parmak frezenin kesici kenarlarını ve yanlış helis açılarını köreltebileceği gibi çapaklara da neden olabilir.
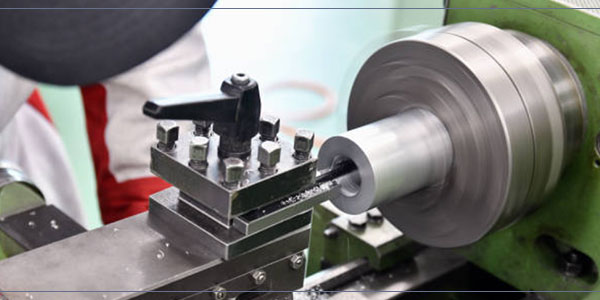
Çapaklar
Çözüm Önerileri
İşleme sırasında çapak oluşumu gözlemleniyorsa, takım için uygun hız ve ilerlemeler yeniden belirlenmeli ve işleme sırasında bu hızların azaltılması düşünülmelidir Ayrıca, yatay frezeleme stratejisi benimsemek ve doğru helis açısı kullanmak da işe yarar çözümlerdendir.
Kötü Bitiş
Nedenleri
Doğru parça bitirme, başarılı bir işleme operasyonu için çok önemli bir göstergedir. Öte yandan, kötü parça bitirme genellikle hurda üretimine ve dolayısı ile baş ağrılarına yol açabilir. Bu durum genellikle çok agresif ilerleme hızlarından ve takım ya da malzeme için çok yavaş hızlardan kaynaklanır. Besleme hızları açısından bakıldığında, agresif kesim derinlikleri parça yüzeyinde izler oluşturarak kötü bitirmelere yol açar. Neticede düzgün bilenmiş takımlar, diğer faktörler doğruysa mükemmel yüzeyler elde edilmesine neden olur. Takım aşırı aşındıysa, parça yüzeyi de zarar görecektir.
Çözüm Önerileri
Düzgün bir parça bitirme için ilerleme hızları ve kesme derinliklerini azaltmak gerekebilir. Artan takım hızı (RPM) de parçada daha iyi bir yüzey elde edilmesine yardımcı olabilir. Son olarak, düzgün bir şekilde keskin veya zamanında yeniden bilenmiş bir takım kullanmak, kötü bitiş sorunlarından kaynaklı baş ağrılarını da hafifletecektir.
Zayıf Boyutsal Doğruluk
Nedenleri
Parça boyutlarının doğruluğu, hem operatör hem de atölye başarısı için çok önemlidir. Zayıf boyutsal doğruluk sorunu ile karşılaşıldığında, operatörün incelemesi gereken agresif kesme derinliği, takım ya da tezgâh rijitliği gibi birkaç alan bulunur.
Zayıf Boyutsal Doğruluk
Çözüm Önerileri
Boyutsal doğruluk sorunlarını çözmek adına atılacak ilk adım eksenel ve/veya radyal kesme derinliklerini azaltmaktır. Sorunun kaynağı zayıf rijitlik ise operatörün, makineyi, takımı, takım tutucuyu ve bağlantı elemanlarını incelemesi ve onarması gerekir. Ayrıca, daha çok kanallı bir takımın kullanımı da bu sorunun çözülmesine katkı sağlayabilir.
Genellikle en deneyimli operatörler bile talaşlı imalatın doğası gereği frezeleme sorunları ile karşılaşırlar. Sorunu doğru bir şekilde belirlemek, bu sorunların uygun çözümü için kritik bir adımdır. Sorunun tanımlanması sonrası, arkasındaki nedeni anlamak ve uygun çözümü uygulamak için bir yol haritasına sahip olunmasını sağlar.