Parça Tasarımını CNC İşleme için Optimize Etmek
Bu Yazıyı Dinleyebilirsiniz.
CNC işleme, yüksek kaliteli sonuçlar üreten çok yönlü bir işleme yöntemidir. CNC işlemenin tüm yeteneklerinden maksimum seviyede yararlanabilmek için, yöntemin güçlü yönleri ve yetenekleri ile uyum sağlayan parçalar tasarlanmalıdır. Bazı temel adımları izleyerek bu süreci daha kolay anlayabilir ve parçaları en iyi şekilde tasarladığınızdan emin olabilirsiniz.
CNC Tasarım Kısıtlamaları
CNC işleme çok yönlü bir yöntem olsa da, sürecin doğasında bazı tasarım kısıtlamaları da bulunmaktadır. Bir parçanın tasarlanma sürecinin henüz başında bu sınırlamaların bilincinde olmak, sürecin ilerleyen aşamalarında sorun yaşamanızın önüne geçebilir. CNC tasarım kısıtlamaları, genel olarak sürecin mekaniği, takım geometrisi ve takım erişimi gibi faktörlerden kaynaklanmaktadır.
1.Takım Geometrisi
CNC kesme takımlarının çoğunluğu silindirik şekilde ve sınırlı bir kesme uzunluğuna sahip şekilde üretilir. Bu takımlar parça yüzeyinden malzeme çıkarırken, sahip oldukları geometriyi işlenen parçaya aktarırlar. Bunun en bariz örneği, işlenen parçanın iç köşelerinin her zaman yarıçapa sahip olmasıdır. Bu durum işlemede son derece küçük bir kesici takım kullanılsa bile geçerlidir.
2.Takım Erişimi
CNC işleme takımlarının sahip olduğu sınırlı erişim aralığı belirli tasarım sınırlamaları yaratır. Kesici takımın iş parçasına doğrudan yukarıdan uygulanması gerekir ve bu açıdan erişilemeyen unsurlar işlenemez. Fakat alttan kesmeler bu kural için bir istisna yaratır. Alt kesimlerin nasıl tasarlanacağına bu makalenin ilerleyen bölümlerinde yer vereceğiz. Takım erişimi, ayrıca büyük bir genişlik-derinlik oranına sahip özellikler işlenirken bir endişe kaynağı haline gelebilir.
Parçanın tüm özelliklerini altı ana yönden biri üzerinde hizalamak gibi önerileri takip etmek, takım erişimi nedeniyle karşılaşılabilecek sorunların önlenmesinde yardımcı olabilir. Beş eksenli CNC makinelerinin mükemmel parça tutma kapasiteleri nedeniyle bu durum başlangıçta çok kısıtlayıcı değildir. Parça üzerinde derin bir çukurun dibine erişilmesi gerektiğinde, uzun şaftlı bir takım kullanmak yeterli olur. Bu yöntem mümkün olmakla birlikte, titreşimin artmasına neden olarak elde edilecek doğruluğun azalmasına neden olur. Parçaların tasarım sürecinde hedeflenen, mümkün olan en uzun çap ve kısa uzunlukta bir takımla işlenebilirlik olmalıdır.
Parça Özelliklerine Göre En İyi Uygulamaları Tasarlamak
CNC işleme, endüstri genelinde kabul görmüş ve kullanılan standartlara sahip değildir. CNC işlemede kullanılan takımlar ve dolayısı ile sahip olunan yetenekler zaman içerisinde sürekli geliştirilmektedir ve CNC işleme parçalarının tasarımı ele alındığında bu belirsizlik bir zorluk yaratır.
Bununla birlikte, daha önce tatbik edilmiş en iyi uygulamalar, parça tasarımında tasarımcıya yardımcı olabilir. Önerilen değerlerin takibi ve teknik fizibilite sınırları göz önünde bulundurularak, yüksek kaliteli bir tasarım oluşturulması sağlanabilir.
1. Boşluklar ve Cepler
Tasarım üzerinde yer alan herhangi bir boşluk için önerilen derinlik, genişliğinin dört katıdır. Bunun nedeni parmak freze takımlarının kesme uzunluklarının bir sınırı olmasıdır. Bu sınır tipik bir kesici takım çapının üç ila dört katıdır. Daha düşük derinlik-genişlik oranları tercih edilirse bu durum titreşimin artmasına, takım sapmalarına ve talaş tahliyesinde sorunlara yol açabilir.
Daha büyük derinliklere ihtiyaç duyulduğunda, bu sorunun üstesinden gelmek için değişken boşluk derinliği tercih edilebilir. Özel takım kullanıldığında, takım çapının boşluk derinliğine oranı 30:1’e kadar tercih edilmesi mümkündür.
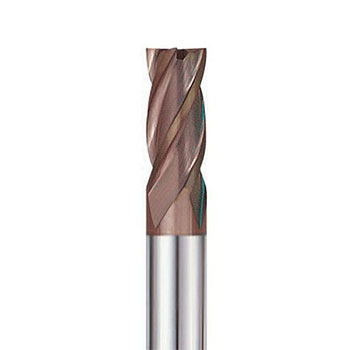
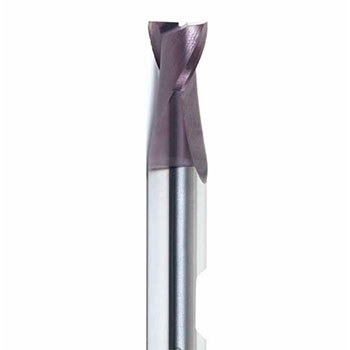
2. İç Kenarlar
İç kenar tasarımlarında, dikey köşe yarıçapı için önerilen değer, boşluk derinliğinin 1/3’ü ya da daha fazlasıdır. Önerilen yarıçapın kullanımı sayesinde, önerilen boşluk derinliği yönergelerini izleyen bir çap aracının kullanılabilmesini mümkün kılar. Önerilen değerden biraz daha yüksek bir değere sahip köşe yarıçapları, 90 derecelik bir açı yerine dairesel bir yol boyunca kesim yapılmasına olanak tanır ve daha yüksek kalitede yüzey kalitesi elde edilmesini sağlar. Bunun yerine 90 derecelik bir açıya ihtiyaç duyulduğunda, köşe yarıçapını azaltma yoluna gitmek yerine T şekilli bri alt kesim kullanmak yerinde olacaktır.
Zemin için önerilen yarıçap 0,5 mm, 1 mm ya da yarıçap yoktur. Fakat herhangi bir yarıçap da teknik olarak uygulanabilir.
3. İnce Duvarlar
CNC ile işlenen parçalarda duvar kalınları için ideal ölçüler, metaller için en az 0,8mm ve plastikler için 1,5 mm olmalıdır. Ancak metaller için 0,5mm ve plastikler için 1mm’lik duvar kalınlıkları da teknik olarak uygulanabilirdir.
Daha ince duvarlar, işleme sürecinde titreşimin artmasına ve elde edilecek doğruluk derecesinde azalmaya sebebiyet verir. Plastik malzemelerde daha ince duvarlar, artık gerilimden kaynaklı olarak eğilebilir ya da sıcaklık artışları plastiğin yumuşamasına neden olabilir.
4. Delikler
Operatörler, delik işleme süreçlerinde matkap uçları ya da parmak freze takımları kullanabilir. Tasarımda yer verilen delik çaplarına karar verilirken, kılavuz olarak metrik ya da emperyal ölçü birimleri ile uyumlu matkap ucu boyutları tercih edilmelidir. Teknik olarak 1mm’nin üzerindeki tüm çaplar uygulanabilir. Delikler sıkı tolerans gereksinimlerine sahipse, operatörler bitirmek için rayba ya da delik işleme takımları kullanmalıdır. 20mm’den küçük, yüksek doğruluk gerektiren deliklerde standart bir çap kullanılması önerilmektedir.
Herhangi bir deliğin maksimum derinliğinin, nominal çapının dört katı olması önerilir ve pratikte bu sayının 40 katı da mümkündür. Genellikle bu oran nominal çapın yaklaşık 10 katına eşittir.
cnc-delık-ısleme
5. Dişler
CNC ile işlenecek parçaların tasarımında kullanılacak diş boyutunun M6 ve üstü olması önerilir. Ancak kullanılabilir olan minimum değer M2’dir. Operatörler, dişleri M6 boyutuna uygun işlemek için CNC diş açma takımları kullanırlar. Bu takımlar kılavuzun kırılma riskini de azaltır. Ayrıca kılavuz ve kalıplar kullanılarak dişler M2 boyutuna kadar kesilebilir.
Diş uzunlukları için önerilen değer nominal çapın üç katına eşittir ve minimum değer ise nominal çapın 1,5 katıdır. M6’nın altındaki herhangi bir diş için, nominal çapın 1,5 katı uzunluğunda dişsiz bir alan deliğin alt kısmına eklenmelidir. M6’dan daha büyük dişler için deliğin tüm uzunluğu boyunca diş kesilebilir.
6. Küçük Özellikler
Tasarıma bazı küçük özellikler eklenebilir ancak bazı iyi uygulamalar aracılığı ile eklenen özelliklerin istenen sonuçları sağladığından emin olmak önemlidir. Tasarımda yer alan herhangi bir delik için minimum 2,5mm çap önerilir. Günümüz atölyelerinde bu çaptaki delikler standart takımlar kullanılarak yüksek hassasiyette işlenebilmektedir.
Konusunda uzman bir operatör, mikro matkap isimli özel bir aletle 0,5mm’lik delikler açabilmektedir.
CNC Makine Toleransı
Talaşlı imalatta tolerans terimi, bir boyutun değişmesine izin verilen miktarı temsil eder. Diğer bir deyişle, bir spesifikasyonun minimum ve maksimum limitleri arasındaki farka tolerans denir.
1. Genel Toleranslar
Bazı şirketler, müşteri kendilerine bir çizim ya da özellik sayfası iletmediğinde genel toleranslar kullanır. Bu toleranslar her şirkette değişiklik gösterebilir. Bazı şirketler varsayılan değerleri dahi kullanmayabilir ve bunun yerine müşteri tarafından bu verilerin sağlanmasını talep edebilirler.
Genel tolerans değerleri belirlemiş olan şirketler, genel ölçüler, et kalınlıkları, kılavuz delik ekleme ve yüzey işleme uygulamaları gibi işlemler için bir takım kriterlere sahip olabilirler. Toleranslar değişiklik gösterse de, tüm boyutlar için genel bir tolerans örneği, metaller için artı-eksi 0,12 mm plastik parçalarda ise 0.25mm’dir.
2. Parça Toleransları
Yapılacak iş için parçalarda uygulanacak toleransların genel toleransların dışına çıkması talep edilebilir. Her parçanın uyum, form ve işlevine göre belirlenecek toleransa dikkat edilmelidir.
Daha sıkı toleranslar, projenin teslim süresini uzatabileceği, hurda malzemeyi artırabileceği ve gerekli durumlarda özel ölçüm araçlarının kullanım gereksinimi doğurarak maliyetleri artırabileceği unutulmamalıdır. Maliyetlerin düşürülmesi için, yalnızca tasarımda yer alan kritik parçalarda sıkı toleranslar uygulanması daha uygun olacaktır.
Boyut Sınırlamaları
Tasarım aşamasında, parçaların genel boyutu önemli bir konudur. Kullanılabilir olan makinelerin yetenekleri ve parçaların özellikleri için gereken kesme derinliği gibi durumlar parça boyutunu sınırlayacaktır. Parça freze ya da torna ile işlenecekse bu hususlar akılda tutulmalıdır.
1.Frezeleme
Frezeleme kullanıldığında, parçanın işlenebilir yüksekliği, parçanın boyutunu ve özelliklerini belirler. İki punta arası açıklık ile işleyebileceği parçaların uygun boyutlarının aynı olmadığı akılda tutulmalıdır. Örneğin, makine Z ekseni boyunca 100 cm hareket edebilir olsa da, o derinlik ya da yükseklikte bir parça işlenemez. Kesim derinliği ve takım açıklığına izin verebilmek için parça boyut ve özelliğinin 75cm’den biraz daha az olması gereklidir.
cnc-frezeleme
2.Torna
Torna ile işlenebilecek en büyük parçanın boyutu, iki punta arası mesafe ve punta yüksekliğine bağlıdır. Canlı takım torna tezgahları ile işleme yapan firmalar, daha kısa teslim süreleri sunabilirken aynı zamanda daha fazla sayıda özelliği parçalara işleyebilmektedir. Üstelik canlı takım torna tezgahları, torna tezgahı içerisinde ayrıca CNC frezeleme kapasitesine de sahiptir.
cnc-tornalama
3.Malzeme
Parçayı üretmekte kullanılan malzemeler, ne kadar iyi işlenebildiğinin yanı sıra maliyetleri belirlemede de kilit öneme sahiptir. Malzeme seçimi yapılırken, optimum performans ile maliyet dengelenmelidir.
Doğru malzemeyi belirlemek için seçilen malzemenin gereksinimleri karşılayacak özellikleri taşıyıp taşımadığı belirlenmelidir. Sertlik, ağırlık, termal kararlılık, kimyasal direnç ve ısıl işleme tabi tutulabilir olup olmadığı gibi nitelikler göz önünde bulundurulmalıdır. İhtiyaç duyulan nitelikler belirlenirken, parçanın işlevleri, çalışacağı ortam, dayanması gereken stres yükü ve parçanın kullanım şekline ilişkin ilgili yönler de tanımlanmalıdır.
CNC işlemede kullanılabilecek birçok farklı malzeme türü bulunur. Ancak metaller ve plastikler bu türlerin en sık kullanılanlarıdır.
1.Metaller
Üreticiler, çelik, alüminyum dahil olmak üzere çok çeşitli metal malzemeyi CNC ile işlenmiş parçalar üretmede kullanır. Alüminyum gibi nispeten yumuşak malzemelerin işlenmesi daha kolaydır ve yumuşak metallerin işlenmesi daha kısa sürdüğünden, bu tür malzemeleri kullanmak genellikle daha ucuzdur. Ayrıca bu tip metaller daha hafif olabilir. Ancak yumuşak metaller, paslanmaz çelik ve karbon çeliği gibi daha sert metallere göre daha düşük stres yüklenebilirler.
Proje gereksinimleri daha yüksek güç içerdiğinde, çelik gibi daha sert metaller tercih edilmelidir. Bu malzemelerin sunduğu dezavantajlar, daha ağır olmaları ve işleme sürelerinin daha uzun olmasıdır. Bu dezavantajlar aynı zamanda proje maliyetlerini de olumsuz etkileyecektir.
Hammadde maliyetleri hemen her projenin nihai fiyatını belirlemede göz önünde bulundurulması gereken önemli bir etkendir.
2.Plastikler
Metallerle karşılaştırıldığında, plastikler daha uygun maliyetli bir seçenek olarak öne çıkarlar. Ancak metallerin sunduğu mukavemet ve sertlik gibi özellikler plastik malzemeler için geçerli değildir. İşlenmesi genellikle kolay olan plastikler, hammadde olarak da metallere kıyasla çok daha ucuzdur. Plastik kullanmanın mukavemet eksikliğinin yanı sıra sıkı tolerans değerlerine ulaşmanın zor olması gibi dezavantajları da vardır. Ayrıca plastik parçalar stres ya da yüksek sıcaklıklar altında deforme olmaya meyillidir. Ancak tüm bu parametreler proje için önemsiz ise, plastik bir malzeme seçmek oldukça mantıklı olacaktır.
Karmaşık Parçalar ve Sınırlamalar
CNC işlemede önemli tasarım sınırlamalarından biri takım erişimidir. Parça üzerinde bulunan birden fazla yüzeye ulaşmak için defalarca döndürmek gerekir. Bir parça her çevrildiğinde, makinenin yeniden kalibre edilmesi ve yeni koordinat sistemi tanımlaması yapılmalıdır. Bu işlemi sıklıkla tekrar etmek, projeyi tamamlamak için gereken süreyi önemli ölçüde artıracağından maliyetleri de buna paralel olarak yükseltecektir.
1.Beş Eksenli CNC İşleme
İşleme sırasında parçayı dört ya da beş kez döndürmek sorun teşkil etmemelidir. Bundan daha fazla döndürülmesi gereken durumlar parçanın daha karmaşık olduğu anlamına gelir ve bu durumda beş eksenli bir CNC kullanmak fayda sağlayacaktır.
Beş eksenli CNC işleme ile işleme süreleri kısalırken daha yüksek yüzey kalitesi sağlayan karmaşık takım yolları takip edilebilir.
Sunduğu ek avantajlara rağmen beş eksenli CNC işleme de diğer yöntemlerle aynı sınırlamalara tabidir. Örnek olarak, iç geometriyi beş eksenli CNC işleme ile de işleyemezsiniz ve daha karmaşık sistemleri kullanmak da oldukça pahalı bir yoldur.
bes-eksen-cnc-ısleme-makınesı
2. Alt Kesimleri Tasarlamak
Standart kesme takımları kullanılırken, bir parçaya doğrudan yukarıdan erişilmesi gerekir. Bu nedenle alttan kesme işlemlerinde özel takımlara gereksinim duyulur.
İki ana alttan kesme türünün her biri için farklı tasarım uygulamaları bulunur. Bunlar T-kanal ve kırlangıçkuyruğu tipi alttan kesmedir.
T-kanal kesme takımları, dikey bir şaft üzerinde yer alan yatay bir kesme bıçağından oluşur. Alt kesimin genişliği 3 ila 40 milimetre arasında değişiklik gösterebilir. Alttan kesme genişliği belirlenirken, tam artışlar ve yaygın olarak kullanılan kesirler kullanılmalıdır.
Kırlangıç kuyruğu kesici takımlar açılarına göre farklılıklara sahiptir. Standart açılar 45 ve 60 derecedir. Bununla birlikte, daha az yaygın olsalar da 5 ve 10 dereceden başlayarak 10 derecelik artışlarla 120 dereceye kadar ulaşan takımlar bulmak mümkündür.
İç duvarda alttan oyulmuş bir parçanın tasarımında, takım için yeterli alan bırakıldığından emin olmak gerekir. Genellikle, işlenmiş duvar ile iç duvarlar arasındaki alt kesme derinliğinin dört katı bir boşluk gereklidir.
Kesme derinliğini sınırlayan standart kesme çapı ile mil çapı oranı, genellikle ikiye birdir. Standart olmayan bir derinlik gereksiniminde atölyelerde özel takımlar oluşturulabilir. Fakat bu durum hem proje teslim süresini hem de maliyetleri artıracaktır.
Uyulması Gereken Genel Kurallar
CNC işlemeye uygun parça tasarımı tamamlanırken, takip edilmesi gereken temel kurallar şunlardır:
- Parça tasarımlarının mümkün olan en büyük takım çapı ile işlenebilecek şekilde tasarlanması gerekir.
- İç dikey köşelere boşluk derinliğinin üçte biri büyüklüğünde pahlar eklenmelidir.
- Genişliğin dört katı kadar derin boşluklar tasarlamaktan uzak durulmalıdır.
- Tasarım özellikleri ile altı ana yön birbirine uyumlu olmalıdır. Bunun mümkün olmadığı durumlarda beş eksenli bir CNC ile işleme tercih edilmelidir.
- Tasarımda toleranslar, dişler ve yüzey kalitesi gibi parametreler yer alıyorsa, tasarıma teknik bir çizim de ilave edilmelidir.